2015 WEEKE CNC machine center Weeke PROFI BMG 211/45/15/AP
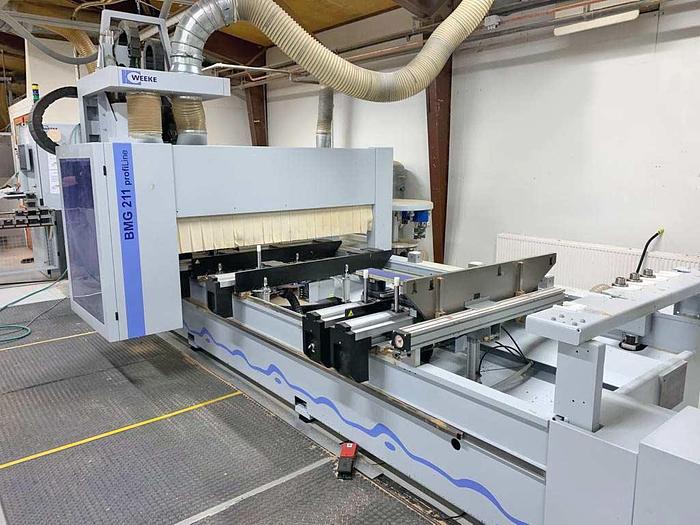
Description
CNC machine center Weeke PROFI BMG 211/45/15/AP year 2015 - Automatic table, size 4,5 m * 1,6 m - Drilling block V12 H4X/2Y - Spindle HSK-12kW, 4-ax = C-ax for aggregates - TC14 places tool changer and TC5 places pick up tool changer - Powertouch control and computer - Barcode reader - Vacuum pump 300/360 m3/hour G.00 PROFI BMG211/45/15/AP CNC-controlled processing centre in moving gantry construction for routing and drilling panels of wood or similar material. Prepared for 1 main spindle, mounted on the right side of the gantry beam. 1. BASIC MACHINE - Solid machine frame in rigid moving gantry execution - Gantry movable in X-direction - Cross support movable in Y- and Z-direction - Paint grey RDS 240 80 05 - Direct extraction of the processing aggregates and separate connection for the extraction device (on site) 1.1 PROGRAM-CONTROLLED EXTRACTION CONNECTION By means of program-controlled assignment the main connection nozzle is assigned to the processing unit. Thus the main connection nozzle is always located straight above the processing unit and guarantees optimum extraction behavior. 2. GUIDING SYSTEM AND DRIVE TECHNIQUE - Dust protected linear guiding system - X-direction: toothed rack drive with servo drive - Y-direction: toothed rack drive with servo drive - Z-direction: ball bearing spindle with servo drive Travel range and speed of the axes: X = see equipment plan Y = see equipment plan Z1 = see equipment plan Z2 = see equipment plan Vector speed X/Y = 110 m/min Z = 20 m/min - maintenance free motors with high resolution optical encoders guarantee high accuracy - digital drive control units guarantee high reliability 2.1 AUTOMATIC CENTRAL LUBRICATION (X) - The X-linear guide blocks and the X-gear racks are automatically lubricated via controlled intervalls. - The components in Y- and Z-axis are manually lubricated. Central lubrication points and a automatic information display on the monitor assist the maintenance. 3. AUTOMATIC POSITIONABLE WORKING TABLE (AP) Automatic positioning vacuum clamping system to clamp coated and uncoated board materials. - The NC-controlled positioning of the consoles is realized via dust protected and high quality linear guides. - The workpiece consoles and the basic vacuum units can be positioned in one direction at the same time. - Adapting the cups and the consoles is realized directly through the last cup position. - A collision control for rest parts between the basic units and the consoles protects the AP-System against damages. - Variable exchanging of the diverse types of vacuum cups is possible. The cup types (rectangular or narrow cups) are programmed in woodWOP. - The system can be adapted manually via pneumatik switches on the workpiece consoles and basic vacuum units. - Programming of the NC-System is realized via the woodWOP programming software. Working table: X = 4500 mm (Length) Y = 1450 mm (Length of WP console) Y = 1350 mm (Travel range of vacuum cups or clamping elements) 1600 mm (Workpiece passage) Z = 125 mm (Thickness) 225 mm (Loading height without vacuum cups) The maximum workpiece thickness to be processed depends on the utilized tool length. Consisting of: 8 in X-direction NC-controlled workpiece consoles incl. 3 basic vacuum units, with travel range 1350 mm, to accept vacuum block cups. 16 vacuum block cups, tubeless, incl. trace valve, manually positionable on the basic units (160x114x100 mm) 8 vacuum block cups incl. trace valve, (for narrow parts), manually positionable on the basic units (125x75x100 mm) 8 rear stop cylinders for workpiece widths up to 1600 mm incl. electrical surveillance of lower cylinder position 8 front stop cylinders incl. electrical surveillance of lower cylinder position 1 pneumatically lowerable side stop system 'PURE STOP' for the working area on the right incl. electr. surveillance of lower cylinder position 1 pneumatically lowerable side stop system 'PURE STOP' for the working area on the left incl. electr. surveillance of lower cylinder position 8 feeding rails of HPL for easy positioning of heavy workpieces mounted on the consoles 2 vacuum generators with a rated capacity of 140/168 m3/h, 50/60 Hz (2x 70/84 m3/h) 4. CONFIGURATION optionally available 4.1 TOOL CHANGE PICK-UP DEVICE Device for automatic feeding of the tool changer. 5. powerControl Modern control system powerControl Hardware: - PLC control according to international standard IEC 61131 - Operating system Windows XP (US) embedded - IntelCore 2 Duo Processor - 17 Inches TFT-flat screen - 1 SATA hard disc minimum 160 GByte - Central USB connection at the operating panel - EtherNet connection 10/100 MBIT RJ4 (without switch) - Provision TeleserviceNet Soft capability Feasibility of remote diagnostics via internet. To this end the customer has to provide a DSL connection. After the guarantee period a corresponding teleservice contract has to be signed for the use of the teleservice. - UPS for the PC (INTERRUPTION-FREE POWER SUPPLY) - Remote terminal with potentiometer and emergency stop switch. powerControl Software: - powerControl CNC-core with: - path control in all axis and parallel sequences by multi-channel technology - look-ahead-function for optimal speed at the transitions - dynamic pre-control for top precise accuracy of the contour - powerControl software package with graphical operating programs: - woodWOP: for graphical, dialogue-oriented generation of CNC-programs - TOOL DATA BASE: with graphical operator guide to manage tool data - PRODUCTION LIST SOFTWARE: for management and creation of product lists for individual manufacturing. Hereby production sequences, target amounts and processing information can be stored - MACHINE DATA RECORDING: for recording of produced workpiece quantities and supervision of the maintenance work - SOFTWARE FUNCTION MOVING Function to manufacture a right program at the left hand workpiece stop and a left program at the right hand workpiece stop - OPTIMIZATION OF SPACE OCCUPATION In this mode processings are optimized in order to save tool changes (in case the processing sequence of the individual programs allow it). Workpiece programs can be combined over the entire table or per each table half. Note: Optimization of space occupation is not possible in production list operation and/or in the case of programs with programmed 'NC stop function'. Copy protection of all software licences via the HOMAG Group licence server. The product must be activated following the installation. Activation via www.eparts.de 6. CE-SECURTIY- AND SAFETY UNITS - ride-along partial encapsulation for the processing units, offers an optimum operating safety and process control - safety barrier at the rear, left and right hand side - The front safety mat is divided in 3 areas for feeding of workpieces in the area which is not active. - Attention: it is not allowed to run the machine without all-around safety barriers - EC conformity (CE) according to the currently valid Machinery Directive for individual machines in operation 7. WEEKE QUALITY PACKAGE - energy guiding chains (cable trail) in X, Y and Z direction in closed execution in order to prevent cable damages caused by residual pieces, chips and so on - linear guidances in X and Y direction are covered with a steel band in order to prevent dirt intrusion 8. ELECTRIC EQUIPMENT: - operating voltage 400 volt, 50/60 Hz (country-specific adaptation of operating voltage by transformer is optionally available) - separate switch cabinet for a positioning on the right or left side in front of the processing table (standard is on the right) - operation terminal integrated in the switch cabinet - prescibed environmental temperature: + 10 degrees up to + 40 degrees Celsius 9. ENERGY SAVING MODE - ecoPlus button for starting stand-by opatio operation. The button can be activated during processing. This will have the following impacts after the end of the program: - Primary power of drives will be switched off - Vacuum pumps will be switched off - When machine is not processing, stand-by operation will be activated after a pre-set time - Activation of ecoPlus sets a potential-free output which can activate the slide (supplied by customer) of an external extraction device 10. DOCUMENTATION - Documentation on DIN A4 paper and digital data medium incl. spare-parts catalog and switch plan. G.0001 Number : 0519 1 off CONFIGURATION EQUIPMENT VENTURE 220 CONFIGURATION V12, H4X/2Y, GS1 X-Y 90°, R1-HSK63-12KW, C-AXIS, TC14 REAR, TC5 PICK-UP V12 HIGH SPEED 7500 incl. quick change system and spindle clamping mechanism Vertical drilling aggregate (separately activated with variable high speed range). Spindle clamping to achieve the drilling depth safely. Working capacity: refer to separate layout Stroke Z-direction: 60 mm Drilling depth: max. 38 mm (up to 55 mm for special borers) Direction of rotation: right hand/left hand Speed: 1,500 - 7,500 1/min frequency controlled Drive: 2.3 kW Shaft diameter: d = 10 mm for quick change system Total length of drill: 70 mm Drilling diameter: max. 35 mm Distance between spindles: 32 mm Type of spindle:individually selectable Arrangement: as per enclosed layout H4X/2Y Horizontal drilling block with 6 spindles which can be activated separately via program Working capacity: refer to separate layout 4 spindles: pitch 32 mm 2 each in X-direction 2 spindles: 1 each in Y-direction Drilling depth: max. 38 mm Drilling height Z-direction: 38 mm from upper workpiece edge Direction of rotation: right hand / left hand Speed: 1,500 - 7,500 1/min frequency controlled Shaft diameter: 10 mm Total length of drill: 70 mm Drill diameter: max. 20 mm Type of spindle:individually selectable GS1 X-Y 90 degrees Grooving saw for processings in X-, Y-direction 90 degrees swivelling Working capacity: refer to separate layout Cutting depth: 30 mm Cross section: max. 70 mm2 Rotation speed: 1,500 - 7,500 1/min frequency controlled Tool diameter: 125 mm Blade width: max. 5 mm R1-HSK63-12KW Automatic tool change spindle in combination with tool change magazine lateral. Working capacity: refer to separate layout Tool holder: HSK63 Tool changing: automatic Direction of rotation: right hand / left hand Speed: 1,250 - 24,000 1/min stepless programmable Drive: frequency controlled AC-motor Max. capacity at the tool: up to 10/12 kW in continuous and intermittent operation (S1/S6 - 50%) Spindle lubrication: permanent grease lubrication Cooling: air cooled Dust extraction:central C-AXIS AGGREGATE INTERFACE (360° interpolation axis) To hold adapter aggregates incl. pneumatic interface and infinitely variable swivel range. C-axis interpolation angle: 360 degrees Torque support: for 3-point-support Gear: slanted toothed pionion gear TC14 REAR Automatic tool change magazine for 14 places Arrangement: moving with the support in X-direction Tool holder: HSK63 Magazine places:14 tool places Tool weight: max. 6 kg incl. HSK holder Tool diameter: max. 130 mm when equipping with 14 routing tools, max. 260 mm with empty places besides Tool change time: approx. 12 - 18 sec. TC5 PICK-UP Automatic tool change magazine for 5 places. Arrangement: lateral fixed mounted to the machine beam on the right hand side Tool holder: HSK63 Magazine places:5 tool places Tool weight: max. 5 kg incl. HSK cone Tool diameter: max. 130 mm when equipping with 5 routing tools Tool change time: approx. 10 - 18 sec. Note: The lateral tool pick-up magazine is not suitable for HSK63 adaptber aggregates. Note: Not in combination with additional tool changing magazines. G.0004 Number : 0720 1 off ADD. VACUUM GENERATOR 70/84 M3/H, 50/60 HZ Additional maintenance-free vacuum generator 100 cbm/with a total capacity of 70/84 m3/h, 50/60 Hz for increase of the vacuum capacity. Use for material with high vacuum transmission. G.0007 Number : 1701 1 off AUTOM. CENTRAL GREASE LUBRICATION DEVICE Automatic program-controlled central lubrication device. The following units are being lubricated automatically: pinion rod X-axis, pinion rod Y-axis, ball screw spindle Z-axis, linear guide X-axis, linear guide Y-axis, linear guide Z-axis. Excepted are the drive units and the individual gears. E.01 Number : 6307 1 off BARCODE READING SYSTEM PACKAGE enables the determination of the production sequence by reading in a 1D or 2D barcode - Barcode software 'woodScan' for preparing the control for automatically taking over up to three barcodes from the barcode reader into the space occupation. For example: name of program, mode of occupation and number of pieces. - incl. wireless hand scanner and base station in industrial design (make Datalogic). - incl. assembly, set-up and functional test at WEEKE - the connection of the barcode reader with the control is effected via separate interface - simple grafical allocation of the barcode information to the machine control when the barcode includes all data necessary for production - customer specific requirements can be realised after clarification upon expense Quality requirements for the barcode min. Degree 3 of the ISO/IEC 15416 Note: Only applicable for individual machines. For machines in a line and cells only in connection with sales no. 6298. E.04 Number : 6318 1 time HOMAG GROUP CONTROL SYSTEM POWERTOUCH - operating panel with FULL-HD Multitouch Display in widescreen format - standardized HOMAG Group operating surface powerTouch - ergonomic touch operation with gestures such as zooming, scrolling and swiping - simple navigation for standardized and intuitive operation of the machine - intelligent display of readiness of production by light function - machine data capturing MMR basic for maintenance depending on need and for the representation of important operating figures (e.g. number of pieces, production time) - expendable to MMR professional for optimization of production by capturing and evaluation of the downtimes of the machine as well as the reasons for disturbances - operating system: Windows 7 professional E.07 Number : 6580 1 off AIR CONDITIONING FOR COOLING THE SWITCH CABINET Air conditioning for cooling of the switch cabinet for a surrounding temperature exceeding 35 degrees C. E.10 Number : 6778 1 off OFFICE PACKAGE PREMIUM (FLOATING LICENSE) Consisting of: - IDENT-No. 6678 woodWOP for external PC (Floating license) - IDENT-No. 6683 woodWOP DXF-Import Basic (Floating license) - IDENT-No. 6690 woodAssembler (Floating license) - IDENT-No. 6694 woodNest Basic (Floating license) - IDENT-No. 6001 3D CNC-Simulation (Single place license for the machine since floating licenses cannot be imported into the machine) - IDENT-No. 6678 woodWOP for external PC (Floating license) - graphical, dialogue orientated CNC-Programming system - easy creation of variant programs by use of variables - graphic tool selection - automatic suction cup recommendation - graphical, dialogue orientated CNC-Programming system - easy creation of variant programs by use of variables - graphic tool selection - automatic suction cup recommendation - woodWOP MOSAIC Software for woodWOP-data administration with graphical preview 'thumbnails' - with this software woodWOP-data files and complete directories can be managed from the graphical point of view - Programs can be administered by drag and drop - woodType Software to generate routing contours for caracters and texts in all available Windows-True-Type-fonts Requirements: Windows XP, Vista, Windows 7, Windows 8 - IDENT-No. 6683 woodWOP DXF-Import Basic (Floating license) - Interface for CAD-data import of 2D-CADprograms to woodWOP - Import of 2D DXF-files - Converting is carried out under fixed profiles (rules). - Display of the geometry, layer and drawing elements. - Creation of the woodWOP program Conditions for the DXF-file: The drawing elements have to be filed on the corresponding layers for differentiation of the processings. The layer should include numeric values for the definition of the Z-axis - alphanumeric layer definition Requirements: Windows XP, Vista, Windows 7, Windows 8 - IDENT-No. 6690 woodAssembler (Floating license) woodAssembler is a program for visualizing of woodWOP programs (MPR) in 3D and enables assembly of single workpieces to complete objects. Including import interface for objects from BLUM Dynalog. woodVisio visualizes objects generated in woodAssembler or Blum Dynalog with surface materials. The objects are displayed in a free-standing position. An expandable library with surface materials is provided. Note: The woodWOP programs must be stored in mpr format. The new file format mprx is not supported. Files can be converted from mprx format into mpr format. - IDENT-No. 6694 woodNest Basic (Floating license) - Software for nesting woodWOP programs - manual positioning and turning around with the mouse - optical distance control Requirements: Windows XP, Vista, Windows 7, Windows 8, woodWOP for the production planning PC Note: The woodWOP programs must be stored in mpr format. The new file format mprx is not supported. Files can be converted from mprx format into mpr format. - IDENT-No. 6001 3D CNC-Simulation (Single place license for the machine since floating licenses cannot be imported into the machine) - Graphical simulation of the CNC-program in '3D' - Time calculation with an accuracy of +/- 10%. - Display of error messages - Display and checking of the positions of clamping elements - Collision check of tools with the workpiece or clamping elements Requirements: Windows XP, Vista, Windows 7, Windows 8 - With a floating license the software can be installed on several workplaces. - With this option max. one user can use the software at the same time (further floating licences are available optionally) Note: - The floating license server is installed on a computer in the customer's net (terminal servers are not supported). supported) - All workplaces have to be interlinked in the customer's net Note: The installation of the software for the process planning workplace and the integration of the machine into the customer network will be carried out by the customer. Optionally supported by our software support (at customer's expense). The product must be activated following the installation. Activation via www.eparts.de Note: Only for the use with new machines! D.01 Service: 8331 1 time DOCUMENTATION AND CONTROL TEXTS: FINNISH Scope of delivery: 1. Display texts for machine operators in Finnish - Operating system dialog in English. Keyboard and dialog input in Finnish 2. Help texts in Finnish 3. Operating manuals in Finnish consisting of operating and maintenance instructions on DIN A4 paper and digital data medium 4. Spare parts descriptions and wiring diagrams in English on digital data medium 5. Keyboard English (Ident Number 6204)
Specifications
Manufacturer | WEEKE |
Model | CNC machine center Weeke PROFI BMG 211/45/15/AP |
Year | 2015 |
Condition | Used |